In the realm of modern manufacturing, CNC (Computer Numerical Control) machining stands out as a revolutionary approach that has transformed traditional methods into a symphony of precision and efficiency. Among the myriad techniques under the CNC umbrella, milling and turning emerge as two of the most prominent players, each showcasing unique capabilities that cater to diverse production needs.
Milling, with its intricate array of rotating cutting tools, carves out complex shapes from solid materials, while turning revolves around the effective manipulation of workpieces, delivering smooth, cylindrical forms. However, the world of CNC machining extends beyond these two, enveloping methods like drilling, grinding, and electrical discharge machining, each contributing its own flair to the manufacturing process.
As we embark on a journey to explore these various CNC machining methods, we will uncover not only their technical intricacies but also their applications, advantages, and the endless possibilities they offer in the quest for innovation and excellence in engineering.
CNC Milling: An In-Depth Look
CNC milling stands as a cornerstone in the realm of precision machining, offering a dynamic interplay of speed, accuracy, and versatility. At its core, this method harnesses a rotating cutting tool to remove material from a solid block, sculpting intricate shapes and features with remarkable finesse. From the artistry of creating complex geometries to producing flat surfaces and unique contours, CNC milling adapts seamlessly across various industries, from aerospace to medical devices. This technique thrives on the automation of multi-axis movements, which allows for the simultaneous cutting of multiple dimensions, thereby enhancing both efficiency and productivity. Whether milling aluminum, plastics, or exotic alloys, the technology\’s capability to fine-tune operational parameters ensures that each product meets stringent quality standards—making it an indispensable asset in modern manufacturing.
When considering cnc machine service, it’s essential to recognize how this technology elevates the manufacturing process. By leveraging advanced automation and precision, CNC milling enables the creation of highly detailed and complex components with unmatched consistency. This service is particularly beneficial when dealing with high-tolerance applications where accuracy is paramount. The ability to customize the milling process to fit specific material properties and design requirements further amplifies its value, ensuring that each piece is crafted to perfection. Embracing CNC machine services allows manufacturers to push the boundaries of what’s possible, delivering superior results in a variety of fields, from intricate medical instruments to robust aerospace parts.
CNC Turning: A Comprehensive Guide
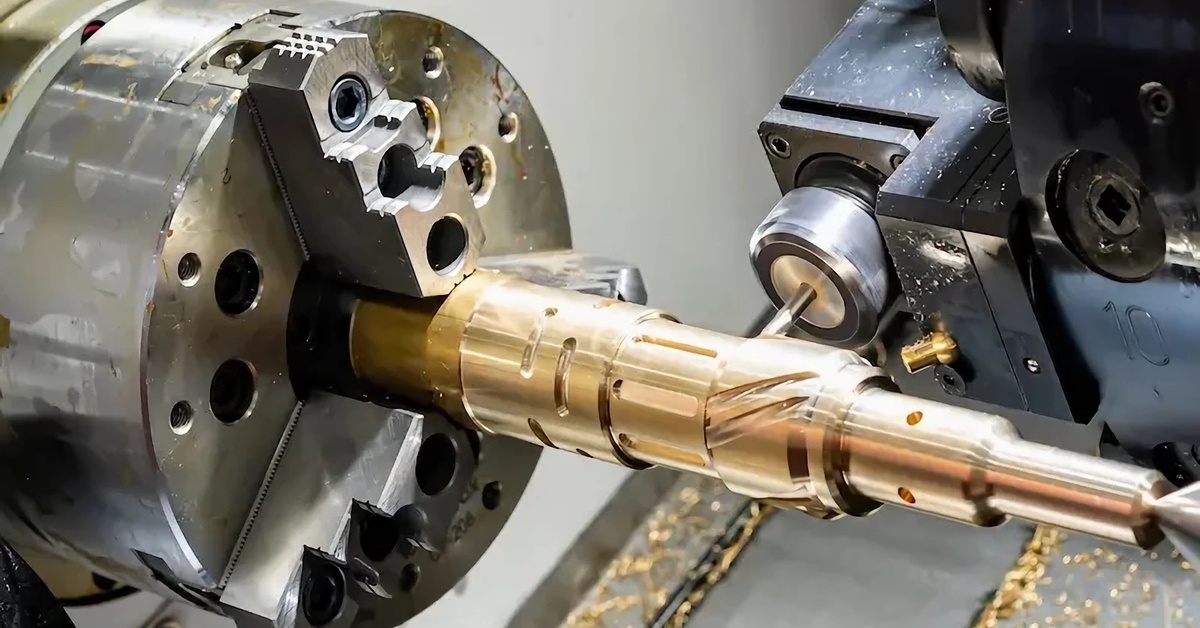
CNC turning stands as a pivotal method in the realm of CNC machining, distinguished by its unique capability to shape materials with precision. This process involves the rotation of a workpiece against a cutting tool, allowing for the creation of cylindrical and conical components with remarkable accuracy.
Whether crafting intricate designs for aerospace applications or producing basic parts for everyday machinery, CNC turning showcases its versatility through a range of complexities. From the initial setup, where tool paths are programmed, to the final touches that ensure each piece meets stringent specifications, every stage is essential.
With the advancement of technology, modern CNC turning machines incorporate sophisticated software and automation, enhancing efficiency and reducing human error. Understanding the nuances of this technique not only enriches ones knowledge of manufacturing processes but also opens doors to innovation in product development, making CNC turning indispensable in todays competitive landscape.
The Future of CNC Machining
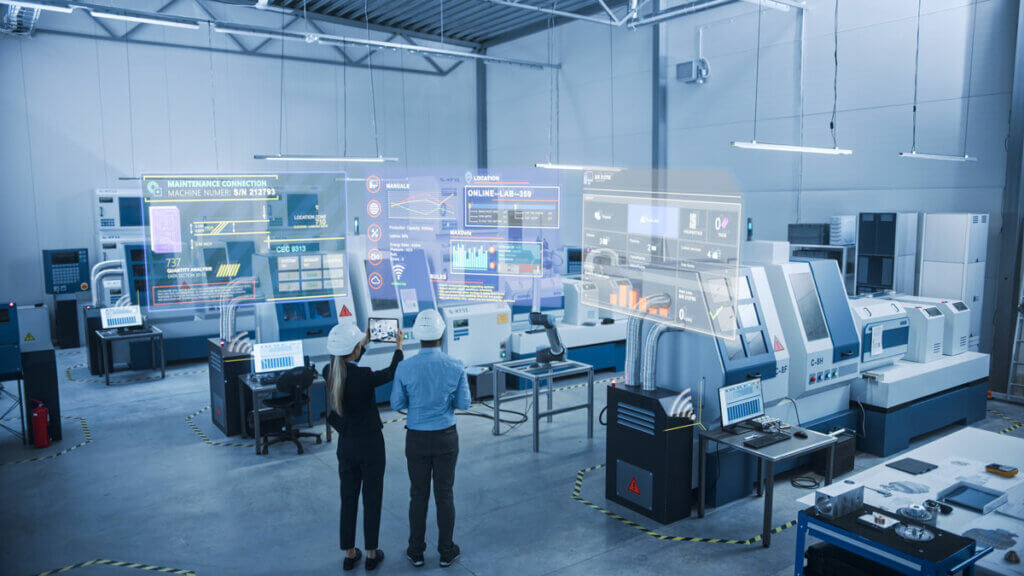
The future of CNC machining is poised to be reshaped by a convergence of emerging technologies and innovative practices that promise to enhance precision and efficiency. As artificial intelligence gains traction, we can expect machines to not only execute complex tasks but also learn from their environment, optimizing processes in real time.
Additive manufacturing, commonly known as 3D printing, is set to complement traditional machining methods, enabling the creation of intricate designs that were once thought impossible. Moreover, the integration of Internet of Things (IoT) devices will facilitate smart factories where equipment communicates seamlessly, reducing downtime and improving workflow.
With advancements in materials science, well likely see stronger, lighter materials being processed, driving industries like aerospace and automotive towards even more ambitious projects. As these elements intertwine, the landscape of CNC machining will not only evolve but also redefine the boundaries of what’s possible in manufacturing.
Conclusion
In conclusion, CNC machining methods such as milling, turning, and others play a pivotal role in modern manufacturing, providing precision, efficiency, and flexibility in producing intricate components across various industries. Each method offers distinct advantages that cater to different project needs, from the versatility of milling to the exceptional accuracy achieved through turning.
As industries continue to evolve, leveraging advanced CNC machine services becomes increasingly essential for businesses looking to maintain competitiveness while ensuring high-quality production standards. Embracing these technologies not only enhances operational capabilities but also paves the way for innovation in design and functionality, underscoring the importance of CNC machining in the contemporary manufacturing landscape.